부쩍 공기가 차가워진 지난 12일 충북 진천군 이월면에 있는 한화솔루션 큐셀부문(한화큐셀) 진천공장을 찾았다. 축구장 26개와 맞먹는 면적인 19만㎡ 규모로 구축된 진천공장은 2016년과 2018년 각각 완공한 1·2공장으로 이뤄져 있다.
진천공장과 인근에 있는 음성공장에서 1년 동안 생산할 수 있는 태양광 셀과 모듈은 각각 4.5GW(기가와트)에 달한다. 이는 620만명이 가정용으로 사용할 수 있는 규모다. 대규모 공장인 만큼 회사에 기여하는 바도 적지 않다. 지난해 진천·음성공장에서 나온 매출만 1조2000억원 규모다.
한화큐셀 관계자들로부터 미래 태양광 기술 로드맵과 진천공장 현황에 대해 간략한 설명을 들은 뒤 2동에 있는 태양광 셀 생산라인으로 들어섰다. 이 생산라인에서는 퍼크(PERC) 셀이 만들어지고 있다. 태양광 셀의 한 종류인 퍼크 셀은 현재 시장의 90%를 차지하고 있을 정도로 대중적이다. 진천공장은 현재 차세대 셀인 톱콘(TOPCon) 셀의 시양산도 진행하고 있다.
오염을 막기 위해 방진복 상의, 헤어캡, 덧신을 착용한 뒤 생산라인에 입장했다. 첫 느낌은 “규모가 상당히 크다”는 것이었다. 장비 하나하나의 규모가 생각보다 크고 제조 공정이 셀 7개, 모듈 8개로 분류되다 보니 장비의 종류도 많았다. 한화큐셀 관계자는 “셀 생산라인만 길이가 300m에 달한다”며 “웨이퍼 입고부터 모듈 출하까지 모든 공정에 자동화가 이뤄져 근무하는 사람은 보기 어렵다”고 설명했다.
장비 내부에서는 로봇 팔이 분주하게 웨이퍼를 옮기고 있었고 자동무인운반차(AGV), 자동화물류반송시스템(AMHS) 등 각종 반송로봇들이 분주하게 움직였다. AGV는 바닥의 노란색 선을 따라 움직였는데, 진로가 사람들에 의해 막히자 위험을 감지한 듯 저절로 멈춰서기도 했다.
셀 생산을 위해 투입되는 회색 웨이퍼는 성인 남성이 손바닥과 손가락을 최대한 편 것과 비슷한 크기의 사각형이었다. 반도체 공정에 투입되는 초록색 원형 웨이퍼와는 모양새가 다르다는 점에서 관심이 갔다.
웨이퍼는 생산라인에서 △웨이퍼 투입·검사 △표면 에칭처리 △N층 확산 △RP막 형성 △반사방지막 형성 △전극 형성 △검사·분류 등 7가지 공정을 거친 뒤 푸른빛을 내는 태양광 셀로 탄생한다고 한다. 셀 생산라인을 둘러보는 데만 20분가량 소요됐다. 한화큐셀 관계자는 “모듈 생산라인도 규모가 비슷하다”며 발걸음을 재촉했다.
흔히 ‘패널’로도 불리는 모듈은 여러 장의 셀을 판에 붙여 만든 제품이다. 셀 자체로는 매우 약해 파손되기 쉬우므로 여러 장의 셀을 붙이고 충격을 버틸 수 있도록 유리, 백시트 등 여러 자재를 결합한다.
12개의 셀을 직렬로 연결해 모듈을 만들다 보니 모듈 생산라인에 있는 장비들은 셀 생산라인에 있는 장비보다 크기가 훨씬 컸다. 길이가 긴 모듈이 장비 안에서 움직이고 장비 밖으로 나와 품질검사를 받는 모습에 눈길이 갔다. 또 공장 내 물류 이동, 작업환경 제어, 불량관리 현황 등을 실시간으로 확인할 수 있도록 곳곳에 설치된 모니터도 눈에 띄었다.
한화큐셀 관계자는 “진천공장에서 볼 수 있는 한화솔루션의 퍼크 셀 제조기술은 독보적인 경쟁력을 유지하고 있다”며 “셀을 반으로 잘라 출력을 높이는 하프셀 기술을 적용하고 제로갭 기술을 활용해 셀 사이 간격을 제거, 같은 면적의 모듈이 더 많은 전력을 생산할 수 있다”고 설명했다.
한화큐셀은 이와 같은 기술경쟁력을 바탕으로 미국을 비롯한 세계 주요 태양광 시장 지배력을 강화해나간다는 전략이다. 이에 더해 내년 톱콘 셀 상업 양산, 2026년 차세대 기술 기반 ‘탠덤 셀’ 양산 등을 통해 태양광 모듈 시장점유율 1위를 공고히 할 것으로 보인다.
진천공장과 인근에 있는 음성공장에서 1년 동안 생산할 수 있는 태양광 셀과 모듈은 각각 4.5GW(기가와트)에 달한다. 이는 620만명이 가정용으로 사용할 수 있는 규모다. 대규모 공장인 만큼 회사에 기여하는 바도 적지 않다. 지난해 진천·음성공장에서 나온 매출만 1조2000억원 규모다.
한화큐셀 관계자들로부터 미래 태양광 기술 로드맵과 진천공장 현황에 대해 간략한 설명을 들은 뒤 2동에 있는 태양광 셀 생산라인으로 들어섰다. 이 생산라인에서는 퍼크(PERC) 셀이 만들어지고 있다. 태양광 셀의 한 종류인 퍼크 셀은 현재 시장의 90%를 차지하고 있을 정도로 대중적이다. 진천공장은 현재 차세대 셀인 톱콘(TOPCon) 셀의 시양산도 진행하고 있다.
오염을 막기 위해 방진복 상의, 헤어캡, 덧신을 착용한 뒤 생산라인에 입장했다. 첫 느낌은 “규모가 상당히 크다”는 것이었다. 장비 하나하나의 규모가 생각보다 크고 제조 공정이 셀 7개, 모듈 8개로 분류되다 보니 장비의 종류도 많았다. 한화큐셀 관계자는 “셀 생산라인만 길이가 300m에 달한다”며 “웨이퍼 입고부터 모듈 출하까지 모든 공정에 자동화가 이뤄져 근무하는 사람은 보기 어렵다”고 설명했다.
셀 생산을 위해 투입되는 회색 웨이퍼는 성인 남성이 손바닥과 손가락을 최대한 편 것과 비슷한 크기의 사각형이었다. 반도체 공정에 투입되는 초록색 원형 웨이퍼와는 모양새가 다르다는 점에서 관심이 갔다.
웨이퍼는 생산라인에서 △웨이퍼 투입·검사 △표면 에칭처리 △N층 확산 △RP막 형성 △반사방지막 형성 △전극 형성 △검사·분류 등 7가지 공정을 거친 뒤 푸른빛을 내는 태양광 셀로 탄생한다고 한다. 셀 생산라인을 둘러보는 데만 20분가량 소요됐다. 한화큐셀 관계자는 “모듈 생산라인도 규모가 비슷하다”며 발걸음을 재촉했다.
흔히 ‘패널’로도 불리는 모듈은 여러 장의 셀을 판에 붙여 만든 제품이다. 셀 자체로는 매우 약해 파손되기 쉬우므로 여러 장의 셀을 붙이고 충격을 버틸 수 있도록 유리, 백시트 등 여러 자재를 결합한다.
12개의 셀을 직렬로 연결해 모듈을 만들다 보니 모듈 생산라인에 있는 장비들은 셀 생산라인에 있는 장비보다 크기가 훨씬 컸다. 길이가 긴 모듈이 장비 안에서 움직이고 장비 밖으로 나와 품질검사를 받는 모습에 눈길이 갔다. 또 공장 내 물류 이동, 작업환경 제어, 불량관리 현황 등을 실시간으로 확인할 수 있도록 곳곳에 설치된 모니터도 눈에 띄었다.
한화큐셀 관계자는 “진천공장에서 볼 수 있는 한화솔루션의 퍼크 셀 제조기술은 독보적인 경쟁력을 유지하고 있다”며 “셀을 반으로 잘라 출력을 높이는 하프셀 기술을 적용하고 제로갭 기술을 활용해 셀 사이 간격을 제거, 같은 면적의 모듈이 더 많은 전력을 생산할 수 있다”고 설명했다.
한화큐셀은 이와 같은 기술경쟁력을 바탕으로 미국을 비롯한 세계 주요 태양광 시장 지배력을 강화해나간다는 전략이다. 이에 더해 내년 톱콘 셀 상업 양산, 2026년 차세대 기술 기반 ‘탠덤 셀’ 양산 등을 통해 태양광 모듈 시장점유율 1위를 공고히 할 것으로 보인다.
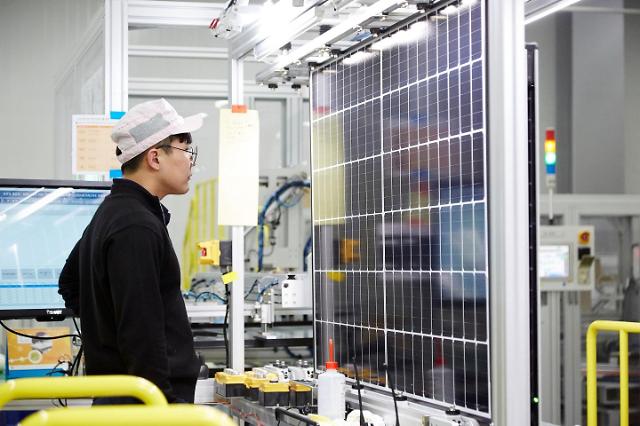
충북 진천군 한화큐셀 진천공장에서 직원이 태양광 모듈의 품질을 검사하고 있다. [사진=한화큐셀]