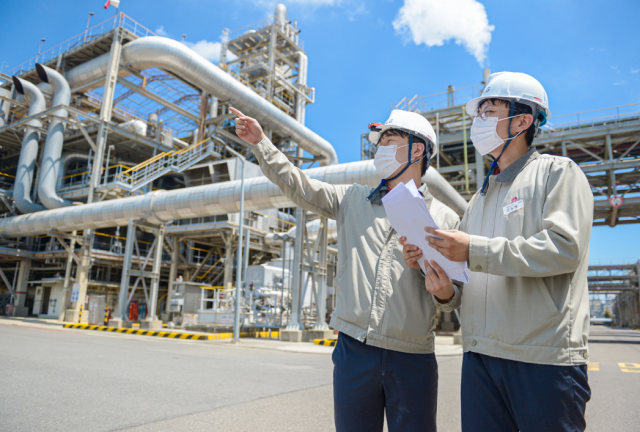
LG화학 여수공장(주재임원 이현규 상무)이 석유화학 산업의 디지털 전환에 박차를 가하고 있다.
작업 효율성 증대 및 산업 재해 감소에 사물인터넷(IoT)과 인공지능(AI), 빅데이터 등의 기술을 이용해 비즈니스를 혁신하는 디지털 변혁(DX)을 산업 현장에 적극 활용한다는 입장이다.
배출가스 연소탑이라고도 불리는 플레어 스택은 공정 중 발생하는 폐가스, 액체 성분이 매연이 되지 않도록 완전히 연소시킨 뒤에 안전하게 배출하는 처리 시설이다.
딥러닝(Deep Learning) 기반의 영상 분석 기술을 적용한 공정 이상 감지 시스템은 해당 플레어스택의 불꽃, 그을음 정도를 자체적으로 인식하여 이상 상황을 감지하고, 연소에 필요한 산소 투입량을 조정하여 잔여 성분이 완전 연소되도록 한다.
기존 공장 운전원이 수동으로 처리하던 사항을 AI가 자체적으로 대응함으로써 생산 효율과 안전성을 높인 것이다. LG화학 여수공장은 현재 운용중인 1개 공장과 더불어 추가 5개 공장에 대하여 올해 상반기 내로 시스템을 확대 적용할 예정이다.
또한 기존 고숙련 작업자의 기술에 의존하여 진행하던 고위험 작업들도 DX가 대체한다. 석유화학 공장은 통상 2~4년의 법적 주기로 공장 가동을 중지하고 전체 설비에 대한 정비를 실시 하는데, 고소·밀폐 작업 등 사고 발생 위험도가 높은 작업들이 수반된다.
해당 정비 과정에 DX를 적용하여 고도 150M의 높은 설비 등 사람의 접근이 어려운 곳을 고성능 드론으로 검사하고, 고압 설비 세정·가압 등의 위험 작업을 완전 자동화 기계가 수행한다.
아울러 생산된 제품의 품질을 검사할 때에도 DX가 적용된다. 제품 이물 분석기가 촬영한 이미지를 AI모델이 분류하여 실타래, 이색 등의 이물을 자동으로 색출한다.
기존에는 기계가 1차적으로 분류한 이미지를 검사원들이 수동으로 재분류하였으나, AI 분류 시스템 도입을 통해 검사원 간 편차를 감소시키고 작업 효율성을 증대하여 품질 신뢰도를 향상시킨다.
LG화학 여수공장 관계자는 “LG화학 여수공장은 제품 생산부터 설비 유지보수, 품질 검사에 이르기까지 생산 라인 전반에 DX를 적용하여 스마트 플랜트(Smart Plant) 구축을 위해 노력하고 있다"며 "사람의 신체적·정신적 한계로 발생할 수 있는 휴먼 에러(Human Error) 방지를 통해 작업 안전성 및 생산 효율성을 확보하도록 하겠다”고 밝혔다.