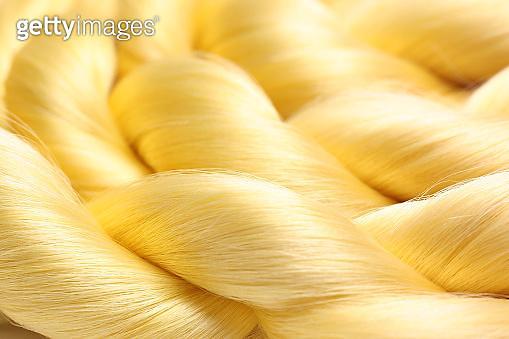
누에고치에서 뽑아낸 실크단백질이 고부가가치 산업으로 떠오르고 있다. [사진=게티이미지뱅크]
실크 단백질은 미국 식품의약국(FDA)에서 인증받았을 만큼 안전성이 입증된 생체 재료다. 체내에 빠르게 소화‧흡수되면서도 안전하기 때문에 건강기능식품으로 주로 이용돼 왔다. 최근에는 특유의 압축‧굽힘 강도가 신체에 적용하기 적합하고, 인체에 무해한 덕에 인공뼈 같은 의료용 소재로까지 활용가치가 넓어졌다.
다만, 실크 단백질의 현장 활용까지 지나치게 오래 걸리는 정부 평가 기간 등 각종 규제는 신속히 풀어야 할 과제다. 기술개발이 끝난 실크 인공뼈의 경우, 의료 현장에 적용되려면 10여년이 걸릴 것으로 보여 이를 단축시키는 것도 관건이다.
전문가들은 국유 특허 등록을 완료한 실크 관련 제품에 대한 정부 규제로 후속 연구가 제때 이뤄지지 못하는 점을 가장 큰 아쉬움으로 꼽았다.
농촌진흥청 등이 추산한 세계 인공뼈 시장 규모는 현재 약 5조 달러(약 6000조원)에 달한다. 임플란트부터 척추까지 신체 모든 골격을 교체하거나 보조‧지지하는 데 인공뼈가 쓰이기 때문에 활용가치가 상당하다.
인공 엉덩이 관절 시장은 올해 90억 달러(약 10조9000억원), 외상고정장치는 110억 달러(약 13조3000억원), 정형외과‧치과 분야는 내년 554억 달러(약 67조원), 인공뇌막‧인공척추뼈 분야는 60억 달러(약 7조3000억원)에 이른다. 매년 두 자릿수 성장세가 이어지고 있어 향후 인공뼈 시장은 더 확대될 것으로 전망된다.
인공뼈에 가장 많이 쓰이는 소재는 티타늄이다. 가볍고 강도가 높은 데다 인체에 무해하다는 장점이 있다. 누에고치의 실에서 분리한 실크 단백질로 만든 인공뼈는 티타늄보다 기능적인 부분은 떨어지지 않는다. 오히려 실크 단백질은 우리 몸을 구성하는 성분인 아미노산으로 돼 있는 만큼 생체친화적이다. 더군다나 인체 내 콜라겐 등 내부 물질 분비를 도와 뼈의 조기 생착에 도움을 줄 수 있어 티타늄 소재보다 훨씬 경쟁력이 있다고 평가받는다.
김응석 국제미용항노화학회 회장은 “어떤 금속이든 생화학적 반응에 따른 마모가 생길 가능성이 있지만, 실크 단백질은 이러한 반응에 안정적이라는 게 가장 큰 장점”이라며 “우리 몸에 더 맞는 소재라는 점에서 매력이 있는 것이고, 장기적으로 연구할 가치가 있는 것”이라고 강조했다.
실크 단백질을 소재로 한 인공뼈 활용 연구는 우리나라에서 가장 활발히 이뤄지고 있다. 실크 단백질 인공뼈 제조기술은 농촌진흥청이 세계 최초로 개발한 원천기술이다. 특히, 최근에는 세계 최고 수준의 원천기술력이 4차 산업혁명의 대표 기술로 꼽히는 3D프린터와 결합해 상용화 가능성이 더욱 높아졌다. 농진청은 이미 ‘바이오 3D 실크프린팅 시스템’을 개발해 놓은 상태다.
이를 통해 환자 맞춤형 뼈고정판과 고정나사‧고정클립 제작이 가능하다. 뼈고정판‧고정나사‧고정클립 등 외상고정장치는 골절 시 사용하는 의료기기로 골절 부위가 다시 붙을 때까지 뼈를 고정하는 역할을 한다. 외상 고정장치 세계 시장은 연평균 8.5% 성장해 올해 110억 달러 규모로 커졌다.
◆뷰티제품부터 의료기기까지 활용도 넓혀가는 ‘실크 단백질’
인공뼈는 실크 단백질을 활용한 소재 제품 중 하나에 불과하다. 실크 단백질은 화장품‧헤어에센스 등 뷰티제품부터 비누‧치약‧구강탈취제, 의료기기인 인공뼈‧고막 등으로 활용된다.
이와 관련된 기술은 △아신씨앤에스 △오마샤리프 △동성제약 △삼성생활건강 △실크로 △파미니티 등 다수의 기업에 이전돼 상용화가 이뤄졌다.
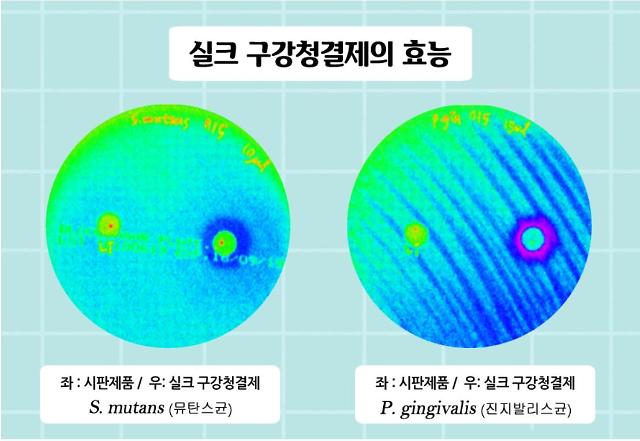
실크 구강청결제 농촌진흥청 실험 결과, 기존 청결제에 비해 살균과 입냄새 제거 효과가 우수한 것을 확인할 수 있다. [자료=농진청 제공]
스펜서바이오 관계자는 “실크 단백질이 세포 재생에 효과가 있어 주로 치과에서 치료 후 사용하는 구강청결제로 활용해 왔으나, 앞으로는 일반 유통에 집중할 예정”이라며 “기존의 구강청결제는 알코올이나 보존제 등으로 구강건조증을 유발하는 경우가 많았는데, 실크 단백질을 이용한 구강청결제는 천연제품으로 이 같은 부작용이 없다”고 설명했다.
인공고막패치와 실크인공뇌막, 인공척추뼈, 실크 수술용 실, 치과용 차폐막 등도 현장 적용 필요성‧가능성이 높은 기술이다.
◆‘세계 최고 수준 기술→사업화’ 지지부진··· 정부 규제 완화 적극 나서야
우리나라가 세계 최고 실크 단백질 기술을 가지고 있지만, 풀어야 할 숙제는 있다. 원천기술을 바탕으로 다양한 산업에 적용될 수 있는 가능성을 보여준 것에 비하면 실제 상용화된 건 많지 않다. 특허청 특허검색시스템 키프리스에 따르면, 최근 5년간 등록된 국내 실크 단백질 관련 특허는 381개에 달하지만, 기술이전부터 제품화에 성공한 건 손에 꼽힐 정도다.
특히 정부의 복잡하고 지지부진한 평가절차와 보험 적용 등의 규제도 ‘세계 최초‧최고 수준 원천기술’의 제품화를 가로막는 요인이다.
실제로 실크 단백질로 만든 인공뼈는 현장에 쓰이기까지 십수년이 걸린다. 우선 가공 기술력이 있는 기업체가 실크 단백질 국유 특허 기술을 활용한 제품을 만들기 위해서는 임상 시험 절차가 필요하다. 임상시험이 끝나면 식품의약품안전처(식약처)의 품목제조 허가를 받아야 한다. 이후 건강보험심사평가원(심평원)에서 그 제품에 대한 보험 적용 여부 판정을 받으면 시중에 풀릴 수 있다. 이 과정이 최소 10년 정도 걸릴 것으로 예상된다.
고막패치는 현재 식약처에 등록이 됐고, 심평원에서 보험 적용 여부를 논의 중이다. 치과용 실크 차폐막은 임상시험을 마치고 식약처 허가를 기다리고 있다.
한 관계자는 “연구 결과가 상용화되기까지 까다로운 심사와 평가를 받아야 하지만, 너무 오래 걸리면 후속 연구가 탄력을 받기 힘들다”며 정부의 평가절차 간소화와 규제 완화 필요성을 역설했다.
권해용 농진청 연구관은 “대학이나 정부, 연구소 단독 연구는 실크 단백질이 어디에 좋다는 사실은 밝힐 수 있으나 실제 현장으로 이어지기가 어렵기 때문에 산‧학‧연 공동연구를 통해 기업의 수요를 바탕으로 연구하는 것이 상용화까지 가장 빠르게 가는 방법”이라고 말했다.