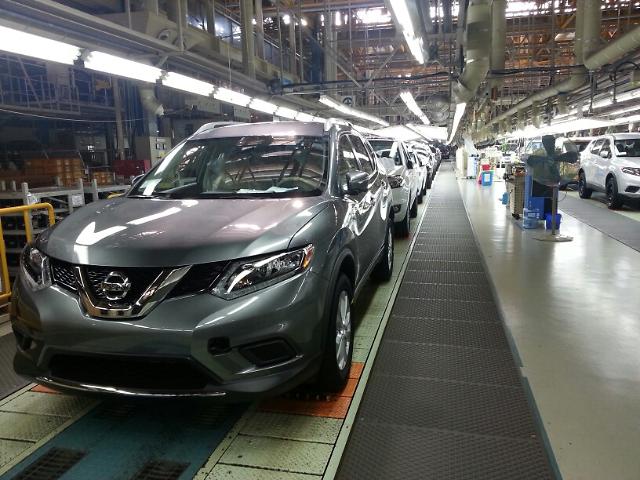
26일 르노삼성자동차 부산공장에서 북미에 수출될 예정인 닛산 로그가 출고를 기다리고 있다. [사진=박재홍 기자]
아주경제(부산) 박재홍 기자 =“우리의 경쟁상대는 현대·기아자동차가 아닙니다. 르노닛산 얼라이언스에 소속된 해외의 다른 공장들입니다.”
지난 26일 부산 강서구에 위치한 르노삼성자동차의 부산공장에서 만난 이해진 생산1담당 상무는 이 같이 강조했다. 일본의 토요타와 미국의 GM, 독일의 폭스바겐 그룹에 이어 지난해 글로벌 완성차 판매 4위를 기록한 르노닛산 얼라이언스 그룹의 해외 공장들이 부산공장의 경쟁상대라는 의미다.
이 상무는 “올해 부산공장에서는 수출 9만2000대를 포함해 총 15만5000대 생산이 예상된다”며 “북미향 로그 생산이 본격화 되는 내년에는 19만대 생산이 예상되고 점차 생산물량을 늘려 오는 2016년 이후에는 지난 2010년 최대 생산량인 27만대를 넘어서는 것이 목표”라고 말했다.
르노삼성차 부산공장은 차량 프레임 및 파워트레인 공장, 그리고 조립공장으로 이뤄져 있다. 이날 찾은 조립공장은 2교대로 시간당 55대가 생산된다고 이 상무는 설명했다.
부산공장에서는 이번 북미지역에 수출하는 닛산 로그를 포함해 SM3, SM5, SM7, QM5, 전기차 모델인 SM3 EV 등 총 6종을 생산하고 있다. 총 2500명의 근무인원 중 1000여명이 조립공장에서 근무하고 있다.
이 상무는 르노삼성의 부산공장은 전 세계 르노닛산 얼라이언스의 공장 중에서도 생산 효율성이 높은 편이라고 강조하며 공장의 한 쪽 벽에 붙어 있는 현수막을 가리켰다.
“이 ‘DSTR 2.1’이라는 숫자는 작업설계 시간 대비 생산에 투입되는 시간을 말한다”며 “현재는 부산공장의 DSTR이 2.2이지만, 2.1을 달성하자는 것이 현수막의 의미다. 향후 이를 1.9까지 줄인다면 전 세계 르노닛산 얼라이언스 공장 중 생산 효율성 TOP 3에 들 수 있다”라고 말했다.
이와 함께 공장 내에서는 라인에서 조립 중인 각종 자동차들과 함께 라인 옆에 레일을 따라 부품을 싣고 이동하는 차량들이 눈에 띄었다.
이 상무는 “이는 ‘AGV(Auto Guide Vehicle·자동 안내 차량)’이라고 하는데 공장 근무자가 차량을 조립하는데 있어 뒤를 쫒아다니며 필요한 부품을 제공해 주는 역할을 한다”며 “다차종을 생산하는 부산공장의 고생산성과 고품질을 유지할 수 있도록 도와주는 역할을 하는 ‘블록&키팅 시스템으로 국내 완성차 공장에서는 최초로 적용된 방식”이라고 강조했다.
AGV는 완성차 1대 당 1차에 필요한 부품을 싣고 작업자를 따라다니는 방식으로 작동한다. 각 박스에는 램프가 있어 라인에서 필요한 부품에 불이 들어오면 작업자가 손쉽게 필요 부품을 꺼내 작업할 수 있도록 해 작업 효율성을 높여 준다고 이 상무는 덧붙였다.
르노삼성차 부산공장은 지난 2009년부터 부분적으로 AGV 시스템을 도입해 지난해부터 전면 도입해 생산에 적용했다.